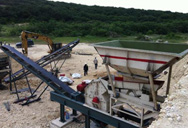
Cement Manufacturing Process | Phases | Flow Chart ...
Aug 30, 2012 · Generally, limestone is 80% and remaining 20% is the clay. Proportioning of raw material at cement plant laboratory. Now cement plant grind the raw mix with the help of heavy wheel type rollers and rotating table. Rotating table rotates continuously under the roller and brought the raw mix in contact with the roller.
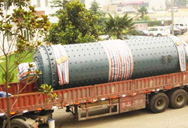
BASIC CEMENT PLANT LAYOUT – Process Cement Forum – The ...
Jul 04, 2020 · BASIC CEMENT PLANT LAYOUT 00. Limestone Quarry and Crushing plant 01. Limestone Stockpile 02. Additives Hopper 03. Additives Storage 04. Raw Mill Building 05. Blending and Storage Silo 06. Preheater 07. Gas Conditioning Tower and ESP 08. Kiln 09. Cooler 10. Deep Bucket Conveyor 11/12. Clinker/Gypsum ...
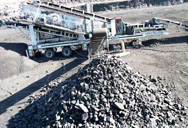
Cement Plant Layout Presentation
Cement Plant Layout Presentation. Powerpoint presentation the cement manufacturing process 1 blasting the raw materials that are used to manufacture cement mainly limestone and clay are blasted from the quarry quarry face 1 blasting 2 transport 3 crushing and transportation the raw materials after crushing are transported to the plant by conveyor
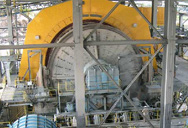
Process Layout Of Cement Plant
Cement Plant Process Layout Truongngo. Cement power plant process layout diagram.Cement plants model railroader magazine model.This plant used a wet process in that the mix was a slurry before it was heated in kilns to produces clinkers the clinkers are ground and mixed with gypsum to produce the cement this is an oversimplification in that the portland cement process has many many …
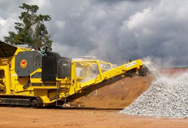
General Layout For Cement Plant Process
We have General Layout For Cement Plant Process,May 10, 2017nbsp018332been widely applied for more than 50 years and so2 abatement is a plant specific issue, the abatement of nox is a relatively new issue for the cement industry. many cement plants have adopted general primary measures, such as process control optimisation, use of modern, gravimetric solid fuel feed systems, optimised cooler …
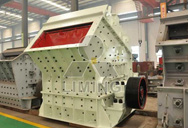
Layout Of Cement Plant
Cement production layout is that at the mine to built of cement clinker production line, in large cities near the cement sales market to establish a new cement grinding plant . Most of the cement admixture is the citys industrial waste generated, new cement clinker grinding plant can greatly digest cities nearby slag, fly ash, slag and other.
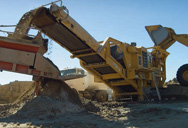
cement plant layout design | Model Railroad Hobbyist magazine
This cement plant on my layout combines kitbashed parts from several kits along with scratchbuilt components. The model ships bulk cement and also receives inbound gypsum and coal. It only requires a few inches of depth along a narrow shelf. Rob Spangler MRH Blog
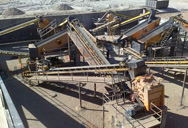
Cement Plant Operations Handbook 5 - Advertisers Preview
9. Clinker – 10. Finish Mill – 11. Cement – 12. Quality Control – 13. Packing and Distribution – 14. Dust Collectors – 15. Maintenance – 16. Process –17. Materials Analysis – 18. Plant Capacity Summary 16. Cement Plant Valuation and New Plant Construction 205 1. Plant Valuation – 2. New Plant …
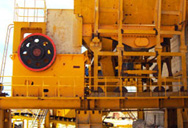
Cement manufacturing - components of a cement plant
Cement manufacturing: components of a cement plant. This page and the linked pages below summarize the cement manufacturing process from the perspective of the individual components of a cement plant - the kiln, the cement mill etc.. For information on materials, including reactions in the kiln, see the Clinker pages.
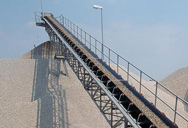
11.6 Portland Cement Manufacturing
Aug 17, 1971 · Sources of PM at cement plants include (1) quarrying and crushing, (2) raw material storage, (3) grinding and blending (in the dry process only), (4) clinker production, (5) finish grinding, and (6) packaging and loading.

Cement Plant Design & Engineering | Cement Manufacturing ...
As a professional cement plant contractor, we have many years of cement plant construction experience and a mature construction process. We can provide you with the most complete and efficient cement production solutions, whether for different production capacity requirements or for different types of cement production.
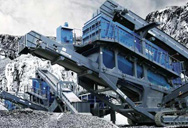
(PDF) PROJECT MANAGEMENT PLAN OF PORTLAND WHITE …
May 10, 2016 · The Cement Plant proj ec t a im s to construct a n ew cem ent producti on plant w ith tw o production li nes, eac h with a production ca pacity of 3,500 tons of c li nker per day . The to tal
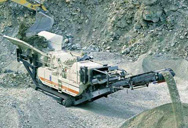
Walthers - Valley Cement Plant - Kit - Overall complex ...
The Walthers Cornerstone Valley Cement kit gives you the structures you need to add a realistic cement factory to your HO Scale steam- or diesel-era layout. Cement is one of the most popular of all building materials. Modern cement is made in special plants consisting of several buildings, each handling a step in the manufacturing process. Various raw materials arrive by rail and are kept ...
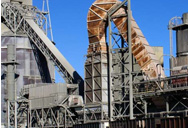
Best energy consumption - International Cement Review
Typical cement plant power costs can range from EUR39 to EUR170/MWh. Mill designs. The most important first step in controlling energy consumption is to be aware of the relative importance of the process areas where most energy is consumed. Figure 2 shows a typical breakdown of electrical energy consumption at a cement plant.
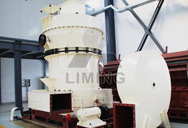
Process duct work - Wikipedia
In the practical design of primarily round structural process ductwork in the cement, lime and lead industries, the duct size involved ranges from 18 inches (45 cm) to 30 feet (10 m). The air temperature may vary from ambient to 1000 °F (515 °C).
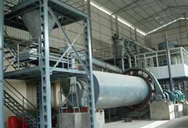
Cement - Penta Engineering Corporation
A trusted resource since 1986, PENTA has provided services to numerous cement plants in virtually every region of the world. Our in-depth knowledge and comprehensive services combined with the extensive experience of our staff allows us to completely develop projects from conceptual design to …
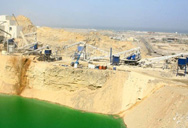
Bulk Cement Plant - Various Projects - MIINC
Bulk Cement Plant - Various Projects Schlumberger Bulk Cement Plant - Shreveport, La MIINC, L.P. was called on to construct the process side of this plant for a configuration first in the 2009 Schlumberger Bulk Cement project in Shreveport. Working from the concepts forwarded by Schlumberger the project helped to establish a design for
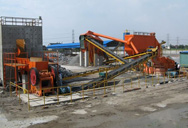
Bridge Gap Engineering
In the 21st Century, when you are looking for cement plant design, time is nearly priceless, and experience is difficult to find…who do you turn to? Bridge Gap Engineering is: Knowledge and Experience Based Solution and Service Focused Bridge Gap is designed on a relationship based business model