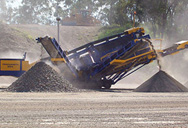
Ball Milling - an overview | ScienceDirect Topics
Ball milling of graphite with appropriate stabilizers is another mode of exfoliation in liquid phase. 21 Graphite is ground under high sheer rates with millimeter-sized metal balls causing exfoliation to graphene (Fig. 2.5), under wet or dry conditions.For instance, this method can be employed to produce nearly 50 g of graphene in the absence of any oxidant. 22 Graphite (50 g) was ground in ...
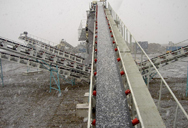
Ball Milling - an overview | ScienceDirect Topics
Ball milling technique, using mechanical alloying and mechanical milling approaches were proposed to the word wide in the 8th decade of the last century for preparing a wide spectrum of powder materials and their alloys. In fact, ball milling process is not new and dates back to more than 150 years. It has been used in size comminutions of ore, mineral dressing, preparing talc powders and many ...
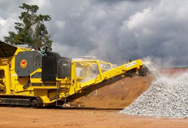
Ball Mill - an overview | ScienceDirect Topics
F. Delogu, G. Mulas, in High-Energy Ball Milling, 2010. 5.2 Fundamentals of mechanical alloying processes in ball mills. A ball mill is a relatively simple apparatus in which the motion of the reactor, or of a part of it, induces a series of collisions of balls with each other and with the reactor walls (Suryanarayana, 2001).
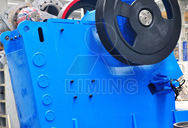
190 questions with answers in BALL MILLING | …
19-7-2020 · Ball Milling - Science topic. Explore the latest questions and answers in Ball Milling, and find Ball Milling experts. Questions (190) Publications (30,233) Questions related to Ball Milling. 1. 2.
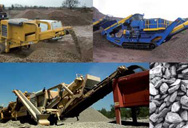
Ball milling: an efficient and green approach for ...
Ball milling: an efficient and green approach for asymmetric organic syntheses Ilya N. Egorov , a Sougata Santra , * a Dmitry S. Kopchuk , ab Igor S. Kovalev , ab Grigory V. Zyryanov , ab Adinath Majee , c Brindaban C. Ranu , * d Vladimir L. Rusinov ab and Oleg N. Chupakhin ab
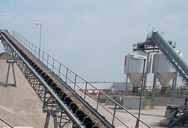
Redox reactions of small organic molecules using …
20-12-2019 · There has also been substantial parallel progress in mechanochemical organic transformations using ball milling (6–18). Since the term mechanochemistry was introduced by Ostwald in 1887, mechanochemical synthesis has been extensively exploited in materials science (6–8), polymer chemistry , and inorganic synthesis , but its application to ...

High-Energy Ball Milling - an overview | …
High-energy ball milling is effective in getting well-dispersed slurry. 7−9 The preparation procedure is summarized in Fig. 24.2.First, commercially available PZT powders (APC 850) were high-energy ball milled to get the desired particle size. Secondly, a selected dispersant was added to the milled powders to get the surface-modified powders.
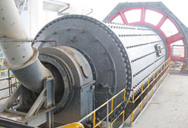
Ball Mills - an overview | ScienceDirect Topics
The ball milling process is carried out for approximately 100–150 h to obtain uniform-sized fine powder. In high-energy ball milling, vacuum or a specific gaseous atmosphere is maintained inside the chamber. High-energy mills are classified into attrition ball mills, planetary ball mills, vibrating ball mills, and low-energy tumbling mills.
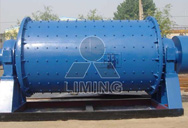
Ball Mill: Operating principles, components, Uses ...
Several types of ball mills exist. They differ to an extent in their operating principle. They also differ in their maximum capacity of the milling vessel, ranging from 0.010 liters for planetary ball mills, mixer mills, or vibration ball mills to several 100 liters for horizontal rolling ball mills.
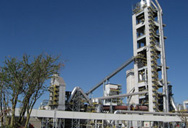
Ball mill - Wikipedia
24-7-2004 · Ball milling boasts several advantages over other systems: the cost of installation and grinding medium is low; the capacity and fineness can be adjusted by adjusting the diameter of the ball; it is suitable for both batch and continuous operation, similarly it is suitable for open as well as closed circuit grinding and is applicable for materials of all degrees of hardness.
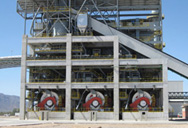
Ball Milling In Material Science - johanklaps.be
Ball Milling In Material Science. Ball mills are among the most variable and effective tools when it comes to size reduction of hard brittle or fibrous materials the variety of grinding modes usable volumes and available grinding tool materials make ball mills the perfect match for a v
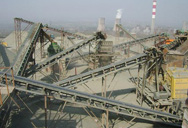
Ball Milling - alpha.chem.umb.edu
Ball milling should be considered as a potentially attractive solution for solvent-free synthesis. 21 Solvent free One-pot process Tip of iceberg . Reference ... Raphael Janot, Progress in Materials Science …
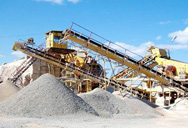
Ball Milling | Scientific.Net
Materials Science Forum ... The effects of different ball milling parameters on the microstructures of composite powders were analyzed. The particle size of graphene coated aluminium composite powder increases with the increase of ball-to-material ratio.
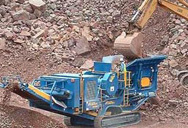
Ball Mill at Thomas Scientific
The Emax is an entirely new type of ball mill for high energy milling. The unique combination of high friction and impact results in extremely fine particles within the shortest amount of time. The high energy input is a result of an unrivaled speed of 2000 min-1 and the optimized jar design.…
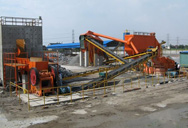
Ball Milling method for synthesis of nanomaterials ...
15-6-2012 · Steps in ball milling method; 1. As the name suggests, the ball milling method consists of balls and a mill chamber. Therefore over all a ball mill contains a stainless steel container and many small iron, hardened steel, silicon carbide, or tungsten carbide balls are …
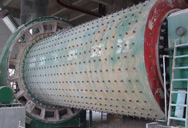
(PDF) DESIGN AND FABRICATION OF MINI BALL …
Since comminution is concerned with liberating valuable minerals for recovery in the separation process, ... Ball milling must be operated in a closed system, ...
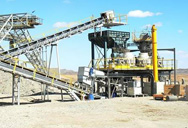
High-surface-area corundum by …
Ball milling of boehmite for 720 min led to the formation of pure α-Al 2 O 3 (Fig. 2A and fig. S4A), showing that these intermediates can also be transformed to the desired corundum phase (alternatively, the remaining diaspore after 180 min of milling can be topotactically converted to α-Al 2 O 3 by a mild calcination at 823 K; Fig. 2A, green diffractogram).
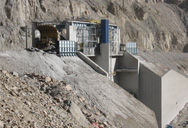
ball milling in material science - do-dampf.de
Rotation of ball mill at critical speedMaterial Science. The material to be disintegrated is tumbled in a container along with wear resistant solid balls in ball milling method. These solid balls hit the material and break them. Ball milling method is used for carbide metal mixtures and cermet materials to perform blending and to reduce ...
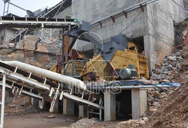
Laboratory Ball Mill - 911Metallurgist
Here is a convertible laboratory ore grinding mill. Use it as a Lab Ball Mill if you like over-grinding or a Rod Mill if you prefer selective milling. Sizes 8″ x 8″ to 8″ x 16″ (ball and rod) Extra Large Batch 12" x 15" (10 kilo ore load) Mild steel construction Cantilever design Integral lifters Bayonet-type lid closure stone seal gaskets Wash screen Motor/reducer and v-belt drive ...
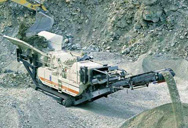
Best way to determine the ball-to-powder ratio in …
Now, in order to get an efficient milling action, 80-110 % of the pores in the ball bed must be filled with the actual particles to be ground. Then, by doing simple calculation, the particles ...