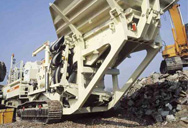
Cement manufacturing - components of a …
Cement manufacturing: components of a cement plant. This page and the linked pages below summarize the cement manufacturing process from the perspective of the individual components of a cement plant - the kiln, the cement mill etc.. For information on materials, including reactions in the kiln, see the Clinker pages. For a more detailed account of the cement production process, see the ...
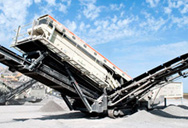
Cement manufacturing - raw materials - …
Cement manufacturing - raw materials. If you happen to be a geologist, the raw materials quarry is probably the most interesting part of a cement works, maybe unless you view the clinkering process as igneous rocks in the making. The most common raw rock types used in cement production are: Limestone (supplies the bulk of the lime) Clay, marl or shale (supplies the bulk of the silica, alumina ...
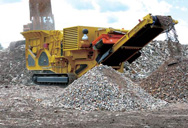
What Is the Cement Manufacturing Process? (with …
03.07.2020 · The cement manufacturing process is completed when the cooled clinker is ground once again in a rotating finishing mill. A combination of gypsum and limestone will usually be added in small amounts to the heated cement during this last grinding step, and coloring agents can also be added here. The fineness of the finished particles will vary according to individual preferences, and the cement ...
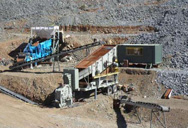
Key facts & figures - CEMBUREAU
Capital intensity: The cost of cement plants is usually above €150M per million tonnes of annual capacity, with correspondingly high costs for modifications.The cost of a new cement plant is equivalent to around 30 years of turnover, which ranks the cement industry among the most capital intensive industries.
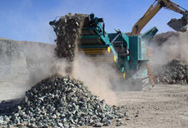
Cement Manufacturing Process | Phases | Flow …
30.08.2012 · Cement Manufacturing Process Phase II: Proportioning, Blending & Grinding. The raw materials from quarry are now routed in plant laboratory where, they are analyzed and proper proportioning of limestone and clay are making possible before the beginning of grinding. Generally, limestone is 80% and remaining 20% is the clay. Proportioning of raw material at cement plant laboratory. Now cement ...

What is the Cement Block in a Parking Lot Called?
What is the cement block in a parking lot called? Let’s find more about these simple but effective devices and the surprising benefits they bring to your parking lot. The Many Names for Parking Blocks. Parking blocks have many different names. Depending on the manufacturer and region, you can call them parking blocks, parking stops, curb stops, and more. No matter the name, the parking block ...
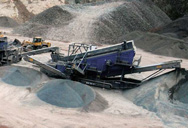
Cement - Wikipedia
Cement manufacture causes environmental impacts at all stages of the process. These include emissions of airborne pollution in the form of dust, gases, noise and vibration when operating machinery and during blasting in quarries, and damage to countryside from quarrying. Equipment to reduce dust emissions during quarrying and manufacture of cement is widely used, and equipment to trap and ...
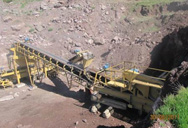
How Cement Is Made - Americas Cement …
Cement is manufactured through a closely controlled stone combination of calcium, silicon, aluminum, iron and other ingredients. Common materials used to manufacture cement include limestone, shells, and chalk or marl combined with shale, clay, slate, blast furnace slag, silica sand, and iron ore. These ingredients, when heated at high temperatures form a rock-like substance that is …
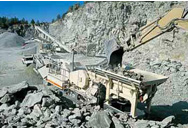
Cement Manufacturing Process: What is Cement …
Cement manufacturing process & what is cement made of, it can be discussed conveniently under two headings: Selection of Raw materials and manufacturing methods. Raw Materials of Cement. Most important raw materials (what is cement made of) required in the manufacture of Portland Cement are: Limestone, Clay, Gypsum, Fuel, and Water (in wet method).

Understanding How The Indian Cement Industry Works
Cement is a bulky material – hence handling this bulky material takes a lot of effort. It occupies a lot of space and carries a lot of weight. Hence higher the distance a cement bag travels, higher is the freight and handling cost involved and lower is the profit a manufacturer makes. Therefore it is important that the manufacturer keeps his production unit as close as close as possible to ...
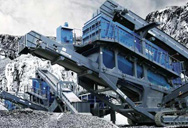
CHEMISTRY OF CEMENT MANUFACTURING - …
Today we are going to start here one very important topic i.e. chemistry of cement manufacturing. We will understand the various terminologies and engineering concepts used in cement technology with the help of this category. Further we will go for discussion of hydration of cement, properties of cement compounds, selection of the process, process technology, burning technology, firing ...
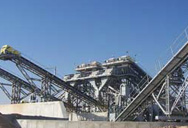
CHAPTER 3.0 CEMENT MANUFACTURING PROCESS
Chapter-3 Cement Manufacturing Process 35 circular manner, layer by layer every day. The limestone is retrieved by cross-sectionally cutting stockpile. Thus, a homogeneous mixture can be obtained after getting deposits from multiple days. So, a pre-lending limestone can be obtained on the stacker. The limestone is stored in a circular or ...
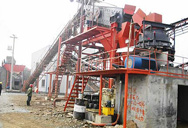
types and manufacturing of cement - LinkedIn …
28.01.2017 · Types of Cement Manufacturing Processes • Wet Process • Dry Process 19. Manufacturing Process of Cement: • Quarry • Grinding • Burning • Grinding • Storage • Packing • Dispatch 20. THE CEMENT MANUFACTURING PROCESS 1. BLASTING : The raw materials that are used to manufacture cement (mainly limestone and clay) are blasted from ...

Cement manufacturing process - LinkedIn …
10.06.2014 · Cement manufacturing process 1. 1.What is cement ? 2.History. 3.Overveiw of Cement Manufacturing process. 4.Overveiw of Kiln process. 5.Why burn wastes ? 2. Portland Cement . A hydraulic cement made by finely powderising the clinker produced by calcining to incipient fusion a mixture of argillaceous and calcareous materials. .Portland cement is ...
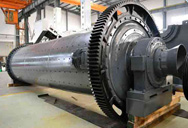
Cements Strength Saves Parking Lot Project
Cement Manufacturing. Cement Industry Overview; Cement Industry Sustainability Manufacturing Program; Cement Industry Annual Technical Conference 2016; Manufacturing Technical Committee ; Environmental Impact Reporting; By Jeff Hawk. When estimators for subcontractor ARS, Inc. bid the Front Range Community College parking lot reconstruction project in Westminster, Colorado, they …
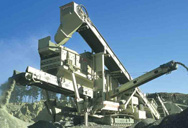
List of 10 Best Cement Companies in India (2020)
04.08.2020 · Till present day, JK Cement has set up a lot of cement manufacturing factories all over India, included by a green field unit in Muddapur, Karnataka. At present, JK Cement has an installed grey cement capacity of 14 MnTPA, making it one of the top cement manufacturers in the country. It has a lot of cement varieties which include JK Super Cement, JK Super Strong Cement, JK White Cement…
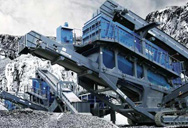
Cement industry in the United States - Wikipedia
The cement industry in the United States produced 82.8 million tonnes (81,500,000 long tons; 91,300,000 short tons) of cement in 2015, worth US$9.8 billion, and was used to manufacture concrete worth about US$50 billion. The US was the worlds third-largest producer of cement, after China and India.The US cement industry includes 99 cement mills in 34 states, plus two plants in Puerto Rico.
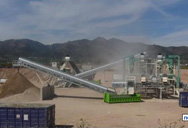
Suez Cement CEO calls for government to …
Jose Maria Magrina, CEO of Suez Cement (HeidelbergCement), has called for the government to set out a plan to rationalise the Egyptian cement market. "There is a large surplus in the market in the last four years," added Mr Magrina. "Therefore, there is a lot of excess supply and very eager ...