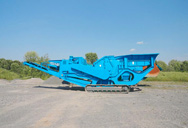
The liberation effect of magnetite fine ground by …
01.07.2012 · Form the above results, it can be found that the liberation effect of magnetite can be improved by fine grinding with the stirred mill and a higher grade concentrate can be acquired from the fine ground product of stirred milling. To verify these results, the raw material (magnetite rougher concentrate) was ground by the experimental stirred mill and ball mill. When grinding to the same …

Quantifying the energy efficiency of fine grinding ...
Quantifying the energy efficiency of fine grinding circuits. Dr Grant Ballantyne . 14 May 2020. In previous publications, we have described how the size specific energy (SSE) can be calculated to predict the energy required to generate new minus 75 µm material. However, if we want to benchmark the performance of fine grinding where the product can be much finer than 75 µm, clearly we require ...
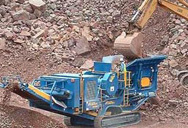
Energy Use of Fine Grinding in Mineral Processing
25.04.2013 · Energy used in grinding activities (U.S. coal, metals, and minerals mining, 2007) 145 ‘‘Best Practice’’ energy use in grinding (U.S. coal, metals, and minerals mining, 2007) 123 Theoretical minimum energy use in grinding (U.S. coal, metals, and minerals mining, 2007) 0.6 Table II. Comminution Equipment, Size Classes, and Grinding Mechanisms
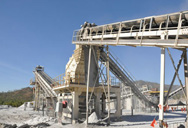
Energy Use of Fine Grinding in Mineral Processing ...
18.12.2013 · Fine grinding, to P80 sizes as low as 7 μm, is becoming increasingly important as mines treat ores with smaller liberation sizes. This grinding is typically done using stirred mills such as the Isamill or Stirred Media Detritor. While fine grinding consumes less energy than primary grinding, it can still account for a substantial part of a mill’s energy budget.
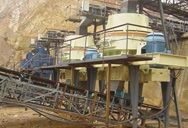
Comparative study of the grinding aid effects for …
01.12.2019 · 1. Introduction. The production of fine particles in the lower micron range by dry grinding processes demands large amounts of energy. For instance, the cement industry alone consumes approximately 12–15% of the world’s total industrial energy, whereby the fine finish grinding of the cementitious products accounts for about 30% of the overall energy consumption (Madlool, 2011).
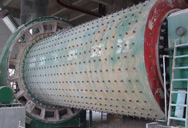
Effect of frictional grinding on ore characteristics …
15.06.2018 · As specific energy required for grinding increases exponentially with product fineness, energy efficiency is always a concern in fine grinding operations (Little et al., 2017). The grinding process is known to be responsible for approximately 50% of the operating costs in a beneficiation plant (Curry et al., 2014).
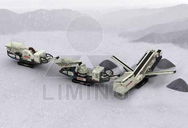
Energy Efficiency - Magnetite
Energy Efficiency Make your windows perform for you and the environment Magnetite ensures your windows will perform for you and the environment. Glass is the greatest source of energy loss in any building, with up to 40% occurring through windows. Our retrofit double glazing is a sustainable investment with no fixed term that offers a range of energy and environmental benefits.
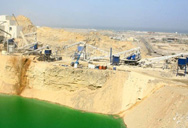
Magnetite - an overview | ScienceDirect Topics
Magnetite, ideal formula Fe 3 O 4, is an intriguing mineral not only because it is magnetic.The formula could be written as Fe 2 + Fe 3 + 2 O 4, which more precisely designates one of its peculiarities.It contains both ferrous (Fe 2 +) and ferric (Fe 3 +) ions, implying synthesis, growth, and stability within an environment where oxidized and reduced states of iron are present and maintained.
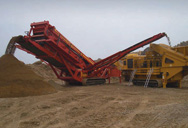
Grind2Energy™ | InSinkErator | InSinkErator US
Organic stone waste is collected and placed into the grind chamber. Grind2Energy grinds stone waste quickly and efficiently. The resulting slurry goes into a holding tank. A liquid waste hauler transports the slurry to a local anaerobic digestion (AD) facility. The AD facility recycles the stone slurry by recovering water and converting captured methane into renewable energy including electricity ...
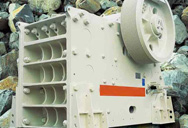
Chapter 12 Comminution Energy and Evaluation …
01.01.2007 · The energy efficiency of comminution is very low and the energy required for comminution increases with a decrease in feed or produced particle size. Research and development to find energy saving and the energy required in comminution processes have been performed. 2. Laws of comminution energy. In design, operation and control of comminution processes, it is necessary to correctly …
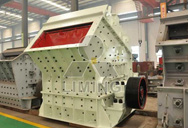
Developments in iron ore comminution and …
01.01.2015 · Conversely, fine-grained magnetite ores require fine grinding, often to below 30 μm, to liberate the magnetite from the silica matrix, incurring greater costs and energy consumption. The comminution energy consumption could be over 30 kWh/t, an order of magnitude higher than for hematite ores. However, with the depletion of high-grade deposits and strong demand for steel, a greater …
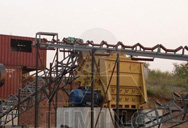
Efficiency of grinding stabilizers in cement clinker ...
01.04.2013 · The overall grinding energy input can be divided into the following groups of effects (Sverak, 2004): (1) ... From the viewpoint of the clinker disintegration process, grinding efficiency is usually specified only within the percentage limits of one-tenth of a unit. Clinker grinding processes exhibit a rapidly growing energy consumption and drop of mill performance with the growing fineness …
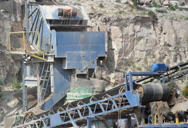
HIGmill - Energy efficient fine grinding - Outotec
HIGmill - Energy efficient fine grinding. Fine grinding using stirred milling is becoming more common in the mineral processing industry. Fine grinding allows liberation of the valuable mineral, which leads to higher mineral recoveries in the process plant. The success of a fine grinding project can be strongly influenced by the energy efficiency, wear part consumption rate and maintenance ...
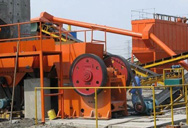
fine grinding energy efficiency magnetite
fine grinding energy efficiency magnetite mill for sale. Chapter 3 Iron Ore Beneficiation Indian Bureau of Mines Hematite and magnetite are the most prominent of . Get Price. isamill fine grinding technology gold. energy efficient magnetite grinding ultra-fine grinding, is an energy-intensive an energy-efficient mineral industry grinding mill that was . Get Price. magnetite grinding ...
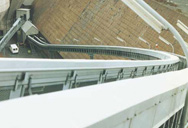
A Comparative Study on a Vertical Stirred Mill …
The effects of operating parameters such as grinding time, stirrer speed, and pulp density on grinding performance was investigated using a magnetite concentrate. Grinding performance was analyzed by considering the product fineness and the energy consumption. The test results show that the grinding time and stirrer speed played a significant role; however, the pulp density had little impact on grinding …
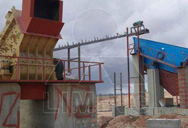
Letters to Editor FINE GRINDING INAUSTRALIAN MIN;ERALS ...
Keywords: stirred mills, fine grinding, energy, particle size, efficiency 1. Introduction A fundamental purpose of comminution in minerals processing is to liberate the constituent mineral that makes up an ore so those valuable com ponents can be separated from the gangue. The effective liberation of val-J.Min.Met. 36 (1-2)A 2000 51. Letters to Editor ues remains one of the major challenges ...
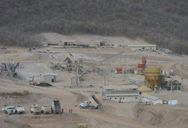
Stirred mills - for wet grinding - liming
Vertimill® energy savings can range from 30% to greater than 50% compared with traditional mills, and the SMD energy savings can be far greater than 50% of ball mill energy in fine grinds. Increased media savings. Increasing energy efficiency means reducing media consumption. Stirred mills use less energy with grinding that results in ...
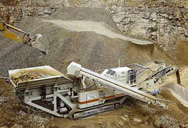
Role of Ferrous Raw Materials in the Energy Efficiency of ...
Role of Ferrous Raw Materials in the Energy Efficiency of Integrated Steelmaking Lawrence HOOEY,1,2)* Johan RIESBECK,1) ... where fine grinding and beneficiation is required to achieve acceptable grades for ironmaking. Sintering dominates in much of Asia and Europe where coarser fines are imported largely from Australia and Brazil. However, there has been a decline in run of mine ore …
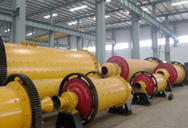
Magnetite: South Australia’s potential
All the magnetite metasomatite deposits in the Mount Woods Domain display a prominent breccia texture, including fine to coarse-grained magnetite in the matrix, and at metamorphic facies ranging from lower amphibolite to granulite (Chalmers 2007). The source of the hydrothermal iron is problematic, with a component possibly of magmatic origin complementing what is inferred to be a significant ...