
Coal Mill Operational Faults - Ball Mill
Coal Mill Operational Faults Coal Pulverizer Monitoring And Analysis A Case Study, It represents the partial work of a project called mill advisor which investigated the common operational and maintenance problems of the coal pulverizer Coal Mill Operational Faults
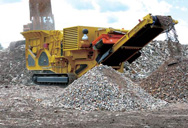
Summary of some faults of coal vertical mill
Summary of some faults of coal vertical mill 1.Excessive coal spillage This is a dangerous situation. A large amount of coal overflow will block the discharge of... 2.The vertical mill continues to run when the outlet temperature is lower than the specified value This is a dangerous... 3.The ...
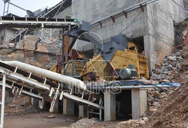
Coal Mill - an overview | ScienceDirect Topics
Operating data from a coal mill is used to compare the fault detection observer-based method and PCA/PLS models based approach. There are 13 process measurements available representing different temperature, mass flows, pressures, speed etc in the coal mill. The measurement is not updated, if the variation is less than 1%.
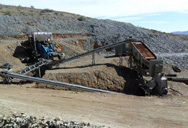
coal mill operation problem
This is all controlled by the coal mill or pulveriser, and its associated feeder equipment. Operation of the coal mill can affect the ramp rate of the power station and its ability to handle rapid changes in output. For coal-fired power plants, the response time of the coal mills is critical for the overall reaction time to changing demand.
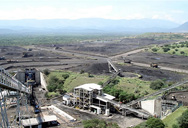
FAULT DETECTION IN COAL MILLS USED IN POWER PLANTS ...
Jan 01, 2006 · This means suppression of disturbances and force the coal mill to deliver the required coal flow, as well as monitor the coal mill in order to detect faults in the coal mill when they emerge. This stone deals with the second objective. Based on a simple dynamic model of the energy balance a residual is formed for the coal mill.
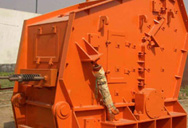
coal mill in power plant problems - Mining Heavy Machinery
coal mill in power plant problems Operation of the coal mill can affect the ramp rate of the power station and its ability to handle rapid changes in output For coalfired power plants the response time of the coal mills is critical for the overall reaction time to changing demand
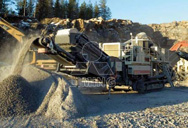
coal mill operational faults - poney-club-poucet.be
coal mill operational faults Fire and Explosion Prevention in Coal Pulverizing Systems · Observer-based fault detection and moisture estimating in coal mills Observer-based fault detection and moisture estimating in coal mills Odgaard, Peter Fogh; Mataji, Babak 2008-08-01 00:00:00 In this stone an observer-based method for detecting faults and ...
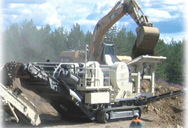
Operating Problem In Palverized Coal Mill-ball Mill
Operating data from a coal mill is used to compare the fault detection observerbased method and pcapls models based approach there are 13 process measurements available representing different temperature mass flows pressures speed etc in the coal mill the measurement is not updated if the variation is less than 1
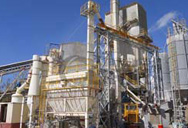
Coal grinding and Firing Systems - HAZOP Analysis - PEC ...
Jan 11, 2016 · Potential hazards, operational problems and design faults are thus identified. The team evaluates the consequences of each deviation and, depending on what safeguards are available in the present system, decides upon recommendations or actions for preventing such occurrences. ... Operation and maintenance engineers as well as coal mill ...
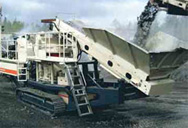
Application of Model-Based Deep Learning Algorithm in ...
The coal mill is one of the important auxiliary engines in the coal-fired power station. Its operation status is directly related to the safe and steady operation of the units. In this paper, a model-based deep learning algorithm for fault diagnosis is proposed to effectively detect the operation state of coal mills. Based on the system mechanism model of coal mills, massive fault data are ...
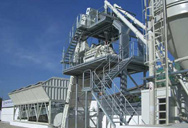
Coal Grinding - Cement Plant Optimization
Coal Mill Operational parameters: Mill Load (Kw or Amps). Mill sound/filling % (in ball mills). Mill Inlet Temperature (0 C). Mill Outlet Temperature (0 C). Gas flow through mill (m 3 /h) or mill fan power (kw) Mill DP, or inlet/outlet draft (mmH2O). Separator DP (mmH 2 O, mbar) and temperatures (0 C). Bag filter DP (mmH 2 O, mbar), Temperature ...
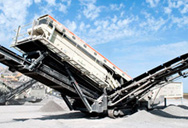
Coal Pulverizer Monitoring and Analysis: A Case Study ...
It represents the partial work of a project called “Mill Advisor” which investigated the common operational and maintenance problems of the coal pulverizer. Combining vibration monitoring and operational parameters such as flow rate, pressure drop and temperature measurement as well as grinding process modeling, this project intends to ...
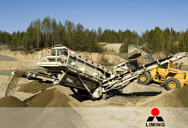
Faults and their effect on coal mining in Illinois
523 FAULTSANDTHEIREFFECT ONCOALMININGINILLINOIS W.JohnNelson IllinoisInstituteofNaturalResources STATEGEOLOGICALSURVEYDIVISION JackA.Simon,Chief CIRCULAR523 1981
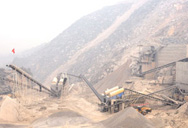
Vertical roller mill services - FLSmidth
Our comprehensive mill services help to identify and eliminate root causes of performance bottlenecks, so that you can prevent: Excessive downtime. Hydraulic system failure. Contaminated lubrication oil. Oil leakage from rollers. Repeated failures. Vibrations.
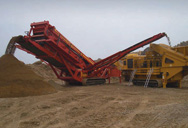
iron ore mill operational problems
iron ore mill operational problems. Biomass applications in iron and steel industry An . A full reduction of iron ore to metallic iron was achieved by 30 wt% of stone dust, as given by Strezov . Although the biomass seems as an efficient reducing agent for iron ore in lab scale tests, the practical application in large blast furnace are still ...