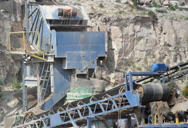
Tunnel Kiln Process Of Iron Ore Reduction
Tunnel Kiln Design For Reduction Of Ore. Direct reduced iron tunnel kiln. Direct reduction of iron ore from tunnel kiln process process the caiman is the professional mining equipments manufacturer in the world, loed in china,india, along with other asian marketplaces to develop and develop, now we get price dri equipment in...
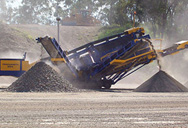
Sponge iron production in tunnel kiln – Aramico …
Although iron powder could be produced in sponge iron tunnel kiln production line and it is the main raw material for powder metallurgy production lines. Process . In sponge iron production plant by tunnel kiln method, after crushing and screening raw materials, iron ore, coal and limestone are mixed and charged in storage bins in certain ratios.
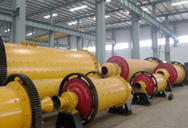
(PDF) Production of Sponge Iron through Tunnel …
Production of Sponge Iron through Tunnel Kiln Process. ... selective reduction of Nb-bearing iron concentrate was achieved by ... the quality of which is directly related to quality of iron ore.
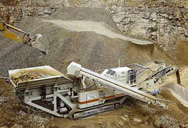
process of iron reduction in tunel kin and rotary …
TUNNEL KILN PROCESS of iron ore reduction – Quarrying Crusher Plant. TUNNEL KILN PROCESS of iron ore reduction … A vertical retort is used for the reduction of iron ore as against a rotary kiln in coal based sponge iron process.
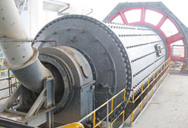
tunnel kiln process iron - katemboservices.co.za
sponge iron tunnel kiln - mvdeburcht.nl. The Nonconventional Method of making Sponge Iron is done in the Tunnel Kiln Process as compared to the Old Rotary Kiln process. In the conventional process of Tunnel Kiln Process, the Iron Ore and Coal are fed in the Crucibles or Saggars of Silicon Carbide and Loaded on the Trolleys.
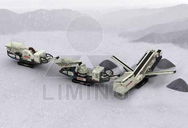
rotary kiln iron ore 1 tph cost in Guyana
May 17 2017Ironmaking in Rotary Hearth Furnace Ironmaking in the rotary hearth furnace (RHF) is a direct reduction process which utilizes non-coking coal for the reduction of iron ore The RHF is the process reactor which consists of a flat refractory hearth rotating inside a stationary circular tunnel kiln
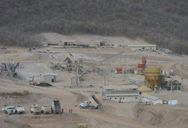
Direct reduced iron - Wikipedia
Process. Direct reduction processes can be divided roughly into two categories: gas-based, and coal-based. In both cases, the objective of the process is to drive off the oxygen contained in various forms of iron ore (sized ore, concentrates, pellets, mill scale, furnace dust, etc.), in order to convert the ore to metallic iron, without melting it (below 1,200 °C (2,190 °F)).
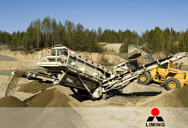
SPONGE IRON PRODUCTION FROM ORE -COAL COMPOSITE …
Keywords: Tunnel Kiln, Iron ore-coal composite pellets, Sponge iron, Thermal efficiency, Carbon utilization efficiency, Percentage metallic iron . 1. INTRODUCTION The tunnel kilns are mostly used by the ceramic industries for heating refractory and ceramic products [1-2]. In the year 1908 use of tunnel kiln started for iron oxide reduction. This
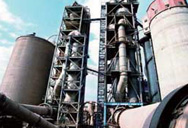
SL/RN process - Outotec
The process principles are the basis for numerous rotary kiln plants and still represent the dominant technology for the direct reduction of lump ore or pellets using coal. Operates with the widest range of iron-bearing materials, such as pellets, lump ore, beach sand, ilmenite and also iron ore …

Coal based Direct Reduction Rotary Kiln Process – …
The metallic iron in this process is produced by the reduction of iron oxide below the fusion temperature of iron ore (1535 deg C) by utilizing carbonaceous material present in the non-coking coal. As the iron ore is in direct contact with the reducing agent throughout the reduction process, it is often termed as direct reduced iron (DRI).
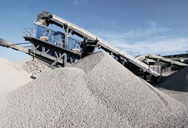
DRI Tunnel Kiln, टनल किलन in Faridabad , CASE …
The iron ore is processed through reduction process by the use of gas that emits from natural coal gas resource. CASE Group of Industries manufactures sponge iron by using tunnel kiln, following reduction of iron ore through Static Kiln Briquetted Iron Technology. The unique SKBITtechnology is gaining.

rotary kiln iron ore - MINING solution
Coal based Direct Reduction Rotary Kiln Process – IspatGuru. The coal based direct reduction rotary kiln process was developed for converting iron ore directly into metallic iron without the melting of the materials. The process has the advantage of low capital expenditure and no requirement of coking coal.
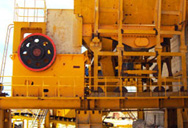
Tunnel Kiln Coal Based DRI Plant, टनल किलन in …
Tunnel Kiln history dates back to 1807 when Hoganas first used this process to produce iron powder of 99.9% purity. When iron ore is mined or processed (in a crusher), lots of fines are generated. Quantity of fines generation is a function of the quality of ore i.e. whether it is hard or soft.
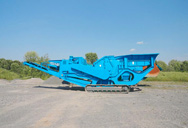
Reduction of iron ore briquettes into DRI in the …
Reduction of iron ore briquettes into DRI in the tunnel kiln process We offer third generation tunnel kiln process from China, to convert soft iron ore lumps or briquetted iron ore fines into Direct Reduced Iron …

Tunnel Kiln at Best Price in India
Sponge Iron, also known as Direct Reduced Iron is the product produced out of using iron ore. The iron ore is processed through reduction process by the use of gas that emits from natural coal gas resource. CASE Group of Industries manufactures sponge iron by using tunnel kiln, following reduction of
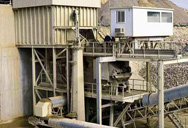
Reduction Efficiency of Iron Ore–Coal Composite …
13-2-2015 · Reduction of iron ore coal composite pellets in tunnel kiln emerges with an edge over all other systems studied. Performance parameters like percentage metallic iron formed, percentage metallization, reduction efficiency, carbon utilization efficiency, energy efficiency have been calculated and found to be significantly higher for composite pellets than the other systems studied.
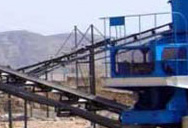
Direct Reduction Process - an overview | …
The MIDREX process is a shaft-type direct reduction process where iron ore pellets, lump iron ore or a combination are reduced in a Vertical Shaft (reduction furnace) to metallic iron by means of a reduction gas (see Figure 1.1.39) [9].
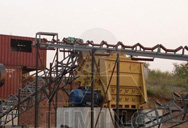
energy efficiency in tunnel kiln dri process
energy efficiency in tunnel kiln dri process . ... automated, intelligen. Raw Complex Gold Ore Processing Machine. Supplier of Raw Complex Gold Ore Processing Machine In ThailandThe 21st century, the rapid ... magnetic separator proceeds for being correctly investigated and made which is broadly employed for removing the iron magnetic supplies ...