
An overview of energy savings measures for …
01.03.2013 · In this paper, energy saving measures in the cement industry, such as energy-efficiency measures for the preparation of raw materials, production of clinker, and the completion of grinding, general energy efficiency measures, and product and feedstock changes are reviewed. The energy-saving measures studied were shown to be effective ways to improve the energy efficiency and reduce greenhouse gas emissions. The amounts of thermal energy savings, electrical energy …
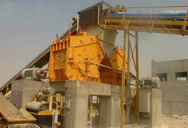
Energy-Efficient Technologies in Cement Grinding …
23.10.2015 · Cement is an energy-intensive industry in which the grinding circuits use more than 60 % of the total electrical energy consumed and account for most of the manufacturing cost . The requirements for the cement industry in the future are to reduce the use of energy in grinding and the emission of CO 2 from the kilns.
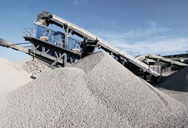
Energy and cement quality optimization of a …
01.07.2018 · Many of the studies focussed on energy assessments of the cement industry to evaluate and then determine the possible energy savings. These reports proved that savings varied between 20% and 50% was attainable by considering the optimization of the existing circuits, evaluation of the possible investments and the changes in the control strategies in the overall production chain [3] , …
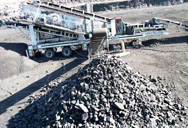
energy saving in grinding circuit in cement plant
Drawing Of Cement Grinding Plant . As old as Cement Industry Popularly used in many Cement plants Tremendous Potential for energy saving,energy saving grinding mill cement making ball mill with ce Thank you for your,Cement Plants Case Study of M/s Mangalam Cement 3410 cm2/gm The saving in energy consumption is more than 6 kWh/ton of Cement BALL MILL CIRCUIT BEFORE .
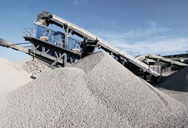
energy saving in grinding circuit in cement industry
energy saving in cement grinding units. cement - energy used in jaw crusher which is a type of highly-efficient and energy-saving energy saving in grinding ,circuit in cement industry >Get Price; energy saving long operation life building Energy ball mill for grinding various ores and other materials are widely 4 213m energy saving cement ball mill >Get Price...
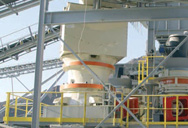
A critical review on energy use and savings in the …
01.05.2011 · Among the different sections, grinding consumes about 60% of total energy consumption in a cement industry. Significant amount of heat is wasted in grinding. Therefore, improvements can be made in this section to reduce heat loss or recycle heat.
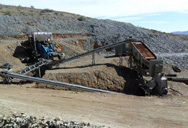
energy saving in grinding circuit in cement …
ball mill for cement factory. In China for 5000t d cement production line using a ball mill with closed circuit Energy Efficiency and Resource Saving Technologies in Cement Industry link Get Price Cement Kilns Size Reduction and Grinding Cement Plants and However at least for early cements the powders were sufficiently coarse that sieve
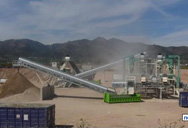
CEMENT GRINDING OPTIMISATION
The electrical energy consumed in cement production is approximately 110 kWh/tonne, and around 40% of this energy is consumed for clinker grinding. There is potential to optimise conventional cement clinker grinding circuits and in the last decade significant progress has been achieved. The increasing demand for “finer cement” products, and the need for reduction in energy consumption and ...
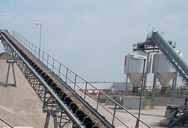
Grinding Circuit - an overview | ScienceDirect Topics
It was found that the high-pressure roll was possible to weaken a variety of materials, including tin, cement clinker, dolomite, coal, copper, and gold ores, and its energy savings was much higher than that of a roll crusher or a hammer mill [45]. Therefore, a significant part of the energy savings in the high-pressure grinding roll can be attributed to the greater proportion of fines produced.
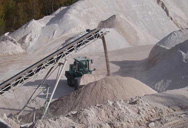
Best energy consumption - International Cement …
For the cement industry, ... etc, are added, the evaluation of the benefits of energy saving investment can become very complex. Typical cement plant power costs can range from EUR39 to EUR170/MWh. Mill designs. The most important first step in controlling energy consumption is to be aware of the relative importance of the process areas where most energy is consumed. Figure 2 shows a typical ...
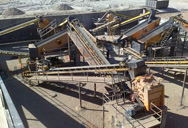
energy saving in grinding circuit in cement plant
energy saving in grinding circuit in cement industry. Energy Efficiency for cement industry Energy Efficiency Energy saving potential on the product cost is estimated to be highest for the Limestone based industry above 19 In clinker based cement industries are estimated to be electricity up to 45 854 MWh could be saved energy saving in grinding circuit in cement industryenergy saving in
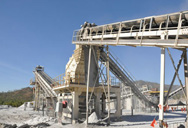
Optimisation of Industrial Cement Grinding …
Optimisation of Industrial Cement Grinding Circuits. Article in Key Engineering Materials 264-268:2173-2178 · January 2004 with 8 Reads How we measure reads A read is counted each time ...

High pressure grinding rolls (HPGR) applications …
01.02.2006 · Open circuit and hybrid HPGR applications can be used to increase the capacity of existing ball mill grinding circuits with slightly less energy consumption. However, substantial energy savings can additionally be obtained using closed circuit HPGR applications in the cement industry.
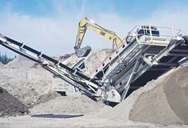
Electrical Energy Conservation in Cement Plants in India
Cement Grinding and Transport Majority of cement mills in India are open circuit ball mills. In some plants closed circuit or VRM are installed. Drives of Grinding Mills and Transport Conveyors consume major power. Packing Plant Drives of packing machines and transport conveyors consume major Electrical Energy, though small in volume compared to other sections of cement plants. Lighting, …
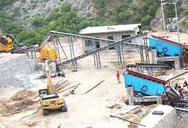
Modern Processing Techniques to minimize cost in Cement ...
lower specific energy than conventional closed circuit ball mills and is being widely used for raw material and coal grinding in the cement industry. The adoption of an external raw material recirculation system has further improved the efficiency of VRM. These mills can also utilise large quantities of hot gases from the pre-heater and even the clinker cooler and thus are able to handle ...
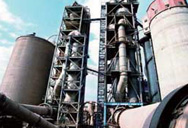
grinding mill in cement plant - Popular Education
Grinding trends in the cement industry - Cement Lime Gypsum In the cement industry, the use of separate grinding plants is currently showing a two-digit annual growth rate. The number of mill vendors has also increased...
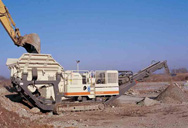
Raw Material Drying-Grinding - Cement Plant …
Grinding Operation Objectives and KPIs: Highly energy intensive unit operation of size reduction in cement industry is intended to provide a homogeneous, dry (<0.5% moisture) and super fine (10-20% residue on 90-micron sieve) raw meal powder for clinkerization process in kiln (Dry Process). Grinding operation is monitored for following parameters to ensure objectivity and economy of operation.
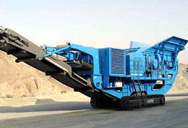
Effect of pre-crushing with a ... - Cement Lime …
Grinding performance and circuit capacity change were investigated when an industrial scale VSI crusher was integrated into the two-compartment ball mill closed circuit. Semi-finish grinding application of a VSI crusher could result in 8 % capacity increase in cement throughput rate and thus, 7 % energy saving in specific energy consumption.
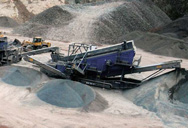
Maschinenfabrik Köppern - Der Spezialist für ...
Energy-saving advanced technology. High-Pressure Grinding The energy-efficiency of crushing and grinding processes is becoming an increasingly important issue for the cement industry. More than half the energy consumed in the industry is used in crushing and grinding operations. One of the main benefits of high-pressure comminution is the reduction in energy requirements when compared with ...