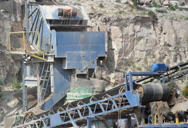
Fine Grinding - an overview | ScienceDirect Topics
For the most part, the grinding energy is derived from the kinetic energy of the media. Increasing the agitation rate increases both the media collision frequency and the impact energy, which leads to higher breakage rates and also extends the range of particle sizes that can be broken.
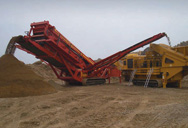
Energy Use of Fine Grinding in Mineral Processing ...
Dec 18, 2013 · While fine grinding consumes less energy than primary grinding, it can still account for a substantial part of a mill’s energy budget. Overall energy use and media use are strongly related to stress intensity, as well as to media size and quality.
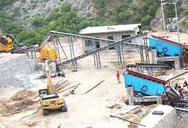
Fine Grinding Services | Ultra Fine Grinding | Fluid Energy
Fine Grinding Services. The process engineers at Fluid Energy recognize that no one jet mill is suitable for all powder processing applications. We therefore employ three jet mill designs, each with its own unique processing characteristics.
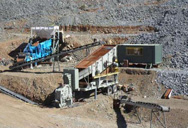
Energy Efficient Fine Grinding - Muzex Machinery
High intensity grinding mills The Outotec 174 HIGmill is an advanced energy efficient fine and ultra fine grinding solution that relies on proven technology The mill can handle increasingly complex ore bodies by taking advantage of gravitational forces and Outotec 174 GrindForce rotor technology to produce a finer grind for mineral liberation
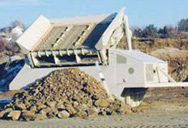
Energy Use of Fine Grinding in Mineral Processing
Apr 25, 2013 · Energy Use of Fine Grinding in Mineral Processing. Energy Use of Fine Grinding in Mineral Processing. JAN DE BAKKER Fine grinding, toP80sizes aslowas7 lm,isbecoming increasinglyimportantasmines treat ores withsmallerliberationsizes.ThisgrindingistypicallydoneusingstirredmillssuchastheIsamillor StirredMediaDetritor.Whilefinegrindingconsumeslessenergythanprimarygrinding,itcanstill account for a substantial part of a mill’s energy …
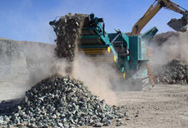
fine grinding reduction
Fine Grinding Services Ultra Fine Grinding Fluid Energy. ... When fine grinding pyritic concentrates of precious metals it is common to follow the fine grinding stage with a pre-aeration stage to remove active pyrite with a reduction in the capital cost of the leach plant. Figure 2 The sizing impact of fine grinding.
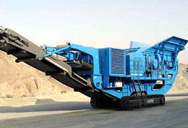
MicroGrinding Systems, Inc. | Energy-Efficient Vibratory Mills
The VKE mill is the most efficient fine grinding mill available. Extremely fast and very energy efficient, the VKE mill is very versatile and can be operated either wet or dry. The air injection system provided with the dry mills can be used to elutriate the material during the grind to pull sized fines out of the mill and allow the mill to grind only oversize material.
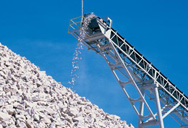
Grinding Machining Process : Complete Notes - mech4study
Dec 23, 2018 · The grinding machine provides high accuracy and fine surface finish with minimum tolerances. The machining process is done by the abrasive action of the grinding wheel; the abrasives are embedded over the periphery of the rotating wheel. In Grinding machine grinding wheel is work as a cutting tool and responsible for all machining processes.
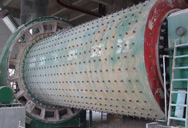
Fine Grinding Corporation
Fine Grinding Corporation. 241 E. Elm Street Conshohocken, PA 19428. Phone: (610) 828-7250. Fax: (610) 828-2584
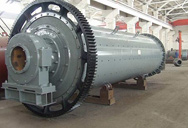
Contract Manufacturing, Powder Milling ... - Fluid Energy
Grinding, Blending, Drying, Screening and more. Fluid Energy is recognized as a leader for Toll Manufacturing in the Powder Processing Industry. Fluid Energy performs blending, jet milling, flash drying and screening operations, producing a consistently high quality product for our customers.
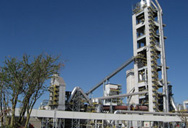
Quantifying the energy efficiency of fine grinding ...
Two of the most popular methods for estimating grinding energy requirements are the Bond operating work index (OWi) and the Morrell specific comminution energy method. Both relate the comminution energy to the reduction in the 80thpercent passing size of the feed and product streams (F80 and P80).
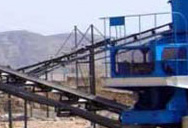
HIGmill - Energy efficient fine grinding - Outotec
Fine grinding allows liberation of the valuable mineral, which leads to higher mineral recoveries in the process plant. The success of a fine grinding project can be strongly influenced by the energy efficiency, wear part consumption rate and maintenance intervals of the selected stirred milling technology.
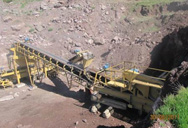
Mill (grinding) - Wikipedia
A typical type of fine grinder is the ball mill. A slightly inclined or horizontal rotating cylinder is partially filled with balls, usually stone or metal, which grind material to the necessary fineness by friction and impact with the tumbling balls. Ball mills normally operate with an approximate ball charge of 30%.
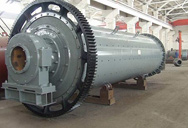
Fluidized Energy Mill: Operating principles, subclasses ...
Pharmaceutical uses of Fluidized Energy mill. a. Fluidized energy is used in milling thermolabile materials. b. It is the choice of mill when a higher degree of drug purity is required. c. Fluidized energy mill is used for the fine grinding of frits, Kaolin, Zircon, titanium, and calcium, alumina. Advantages of Fluidized Energy mill. 1.
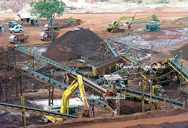
Energy efficient fine grinding with Outotec HIGmill ...
At the target grind size of 40µm, the required Specific Grinding Energy for flat discs is 22.7 kWh/t and for GrindForce rotors it is 16.3 kWh/t, a 28% energy saving. Recently Outotec has conducted rotor design optimisation work at the same site and achieved a further 5% decrease in energy use.

Visual Encyclopedia of stone Engineering
Pulverizers, also know as fluid energy mills, are used for fine grinding and close particle size control. They are primarily used when contamination-free products are desired. General Information There are two main classes of pulverizers: air swept pulverizers and air impact pulverizers.
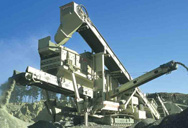
Grinding Discs for Metal | 3M Metal Sanding Discs | 3M ...
Our selection of sanding and grinding discs for metal brings the quality and performance of 3M abrasives to a variety of hand-held applications. With our innovative Cubitron™ II Abrasives Discs, 3M has rewritten the rules for speed, consistency and abrasive lifespan in aggressive applications.
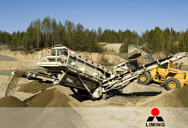
IsaMill - Wikipedia
The grinding action is by attrition and abrasion, in which very fine particles are chipped from the surfaces of larger particles, rather than impact breakage. This results in the generation of fine particles at greater energy efficiency than tumbling mills.