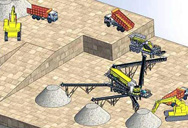
The Sintering Process of Iron Ore Fines – IspatGuru
Sintering is a thermal process (carried out at 1300 deg C to 1400 deg C) by which a mixture of iron ore, return fines, recycled products of the steel plant industry (such as mill scale, blast furnace dusts, etc.), slag forming elements, fluxes and coke fines are agglomerated in a sinter plant with the purpose of manufacturing a sintered product of a suitable stone composition, quality ...
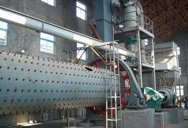
sintering of iron ore fines in steel plant
iron ore sinter for chinese steel plants. sintering of iron ore fines in steel plant - Mine , 211 General Information on Emissions from Iron Sintering Plants Sinter plants that are located in a steel plant recycle iron ore fines from the raw material storage and handling operations and from waste iron oxides from steel …
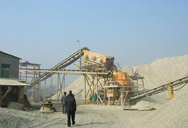
Sinter plant - Wikipedia
Sinter plants agglomerate iron ore fines (dust) with other fine materials at high temperature, to create a product that can be used in a blast furnace. The final product, a sinter, is a small, irregular nodule of iron mixed with small amounts of other minerals. The process, called sintering, causes the constituent materials to fuse to make a single porous mass with little change in the stone properties of the ingredients. The purpose of sinter are to be used converting iron into steel.
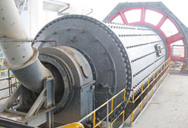
Sintering Of Iron Ore Fines In Steel Plant
Sintering pot test and plant test with the addition of robe river ore fines based on the ra 100083,chinaapplication of pilbara blend iron ore in shougangjiron steel2009-0. Read More New Insights Into Alumina Typesin Iron Ore And Theireffectonsintering
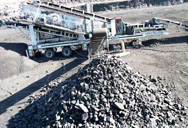
Sintering: A Step Between Mining Iron Ore and …
The only source of primary iron is iron ore, but before all that iron ore can be turned into steel, it must go through the sintering process. Sinter is the primary feed material for making iron and steel in a blast furnace. According to the U.S. Environmental Protection Agency, the sintering process converts fine-sized raw materials, including ...
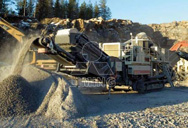
Ore Sintering - an overview | ScienceDirect Topics
02-04-2010 · Iron ore sintering is a material preparation process employed worldwide in the production of iron and steel. According to statistical data on pollution, sintering plants rank second in terms of toxic emissions, after the incineration of municipal solid waste ( Menad et al., 2006; Remus et al., 2013 ).
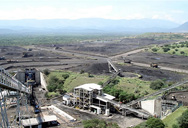
CHAPTER-11 FUNDAMENTALS OF IRON ORE SINTERING
FUNDAMENTALS OF IRON ORE SINTERING R. P. Bhagat INTRODUCTION The process of sinter making originated from a need to make use of fines generated in mines and in ore benefiCiation plants. With the development of sintering technology, a sintering plant has become a tremendous success for providing a phenomenal increase in
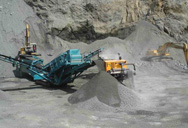
Modeling Sintering Process of Iron Ore
Modeling Sintering Process of Iron Ore Jose Adilson de Castro Graduate Program on Metallurgical Engineering -Federal Fluminense University Brazil 1. Introduction In this chapter, a methodology for simulating th e sintering process of iron ore is presented. In order to study the process parameters and inner phenomena, a mathematical model
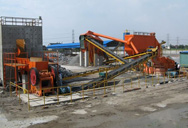
SINTERING AND PELLETISATION OF INDIAN IRON ORES
Catering to the iron ore demands of all the DR/ Steel plants in the country Good productivity, product quality and reasonable campaign life is very important amongst fierce competition and low grade iron ore availability. To meet ever increasing demand for iron ore with growth in Steel …
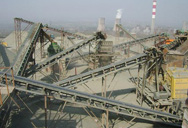
Iron Ore Agglomeration Processes and their …
Fine grained iron ores are pressed in to pillow shaped briquettes with the addition of some water or some ... Briquetting and nodulizing are cold binding processes and mostly used for the recycling of recovered iron ore wastes in the steel plant. Sintering and pelletizing are the processes of major ... History of sintering of iron ore.
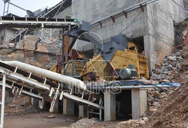
Sintering of Iron Ore Fines, and Raw Materials for …
A detailed study has been made at the National Metall-urgical Laboratory on the sintering charactersitics of the iron-ores of Rajharapahar. Madhya Pradesh, and other raw materials likely to be used in the Bhilai steel plant. The effects of variables such as coke and moisture contents in sinter mix, basicity and raw material proportions, on the sintering time and their effects on the quality of ...
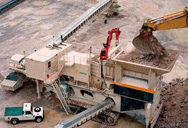
Iron Ore to Sintering to Steelmaking - Analyzing …
18-06-2019 · U.S. iron ore production was estimated to have increased in 2018 owing to increased steel-mill-capacity utilization and higher steel demand. Raw steel production increased to 86.6 million tons in 2018 from 81.6 million tons in 2017. But before all that iron ore can be turned into steel, it must go through the sintering process. Sinter is the ...
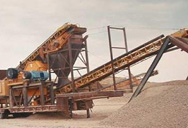
PROCESS BRIEF - Ministry of Steel
This code of safety is applicable to Sinter manufacturing plant as well as Sinter Plant Dept.of an Integrated Steel Plant. 3. PROCESS BRIEF Sintering process is developed mainly to utilize under size of lump ore called iron ore fines; which otherwise, could not be charged directly in blast furnace. In
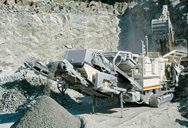
CHAPTER-1: INTRODUCTION
The iron ore advantage for Indian steel plants will remain as long as there is sufficient iron ore available within the country. It is estimated by the steel industry that at the present steel output growth, ... While the sintering process utilizes ore fines in the size range of minus 10mm to 0.15 mm, ...
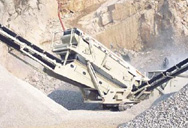
(PDF) Iron Ore Sintering: Process - researchgate.net
Sintering is a thermal agglomeration process that is applied to a mixture of iron ore fines, recycled ironmaking products, fluxes, slag-forming agents and solid fuel (coke).
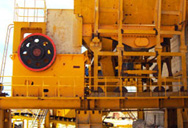
030301 Sinter plants - European Commission
Sinter plants 73 030301 Sinter plants Process description By sintering, the pelletisation of fine-grained, smeltable ores, iron ore in particular, to compact lumps by heating nearly to the melting or softening point is understood. Melting tendencies at the stone boundaries lead to a caking of the material.
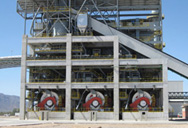
Iron Ore Sinter - an overview | ScienceDirect Topics
The effect of iron ore characteristics on sintering is mainly through their impact on the granulation and densification processes. With the rapid change in iron ore supplies and composition, steel mills now have to adjust the composition of the ore mixture to their sinter plants more frequently than ever before. Hence, different scales of test ...
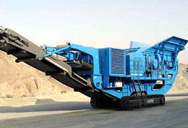
Iron Ore Sintering Pelletiing Process
The Sintering Process Of Iron Ore Fines Ispatguru. 2020-6-27Iron ore pelletiing systems liming. Iron ore fines are agglomerated into pellets and then indurated using a furnace to create iron ore pellets. These are typically fed to a blast furnace or DRI plant as part of the process to make steel. Sintering And Pelletising Process. Read More
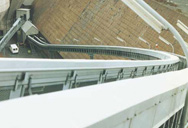
in the field of Iron Ore Sintering The Role of Mixing ...
in the field of Iron Ore Sintering Dipi. Ing. Guenther Brandes Dr. Hans Rausch l R1N(, the last twenty ^ears it has increasingly D been realised that the sintering plants, far from beiirg just a necessary evil, are in fact an essential part of the metallurgical installations of a blast furnace plant capable of contributing to consi-